As the fervour of the Industrial Revolution began its sweep across a turbulent, troubled Europe in the mid 19th Century, vast numbers of its people saw an opportunity to escape across the ocean.
Tens of millions of Europeans sought personal freedom and economic opportunity in the New World, sailing the Atlantic in small sailing ships and suffering squalor, disease, and mistreatment as they did. In the 1840s alone, around 1.5 million of those people were from one place: the lands we now know as Germany.
War-torn, undemocratic, and yet to be united into a single nation, conditions in their homeland were almost as dire as they were aboard the ships. However, in 1847, a group of enterprising shipowners and merchants in the port-city of Hamburg decided to change that decisively.
They created a new ocean liner company, one that chose to see passengers as people – as customers – rather than human freight. It was a company that would transport people from Hamburg to New York and do so on a founding promise of quality service.
They called it Hamburg-Amerikanische Packetfahrt-Actien-Gesellschaft – or HAPAG, for short. Its first ship, the Deutschland, set sail the following year.
Today, the company’s descendent – Hapag-Lloyd – is the fifth largest shipping company in the world. Born in the twin cauldrons of industrial and political revolutions, it is now undertaking a new, root-and-branch, digital revolution all its own.
The standard unit of measurement for shipping companies is the TEU – or Twenty-foot Equivalent Unit; one 20ft (6.1m) container equals one TEU. In 2022, Hapag-Lloyd moved 11.8 million of them across the seas with its fleet of 264 ships. The company operates in 135 countries and employs more than 16,000 people.
The last decade has seen a wave of consolidation in the global shipping industry, with Hapag-Lloyd a key driver of the change; it is five times larger today than it was in 2005. But more recently it has confronted – along with the rest of the industry – a series of exceptional challenges.
COVID-19 fundamentally disrupted supply chains throughout the world, first when countries locked down and then when demand surged to unprecedented levels as the pandemic waned. In the midst of that, the grounding of one of the world’s largest container ships in the Suez Canal in 2021 added a new crisis to the mix. One of the world’s most important shipping lanes had been plugged, piling up a queue of almost 400 ships and nearly $10 billion worth of trade. For shipping companies like Hapag-Lloyd, it meant an emergency response on an unprecedented scale.
That the company weathered all these storms successfully was due in no small part to a digital transformation process it had begun in earnest some years earlier. And at the heart of that transformation was automation.
Automation for transformation
The company’s digital ambitions formed a key component of its grand ‘Vision 2023’ strategy, announced in 2018. The plan set out an overall goal entirely in keeping with that original promise to its first emigrant customers: Hapag-Lloyd would become ‘Number One for Quality’.
Far from being an empty statement, the company unveiled a raft of factors that would contribute to achieving that goal, and committed to measuring and reporting its progress against them publicly and transparently. Enabling that vision would be a holistic digital transformation to empower staff to make faster, better, data-led decisions and deliver enhanced services more efficiently.
“The shipping business is very price competitive. So, we strongly believe that better service is the way we can differentiate from competitors. But we want to be very specific in measuring what that means for customers,” explains Javier Verstraete who, as Senior Director, Global Business Support at Hapag-Lloyd, helps lead the company’s digital transformation mission.
“We are laser focussed on quality. Without technology as an enabler, you will not do it. Business and IT go together. In all these quality promises we are doing, in each of these, you have a lot of automation.”
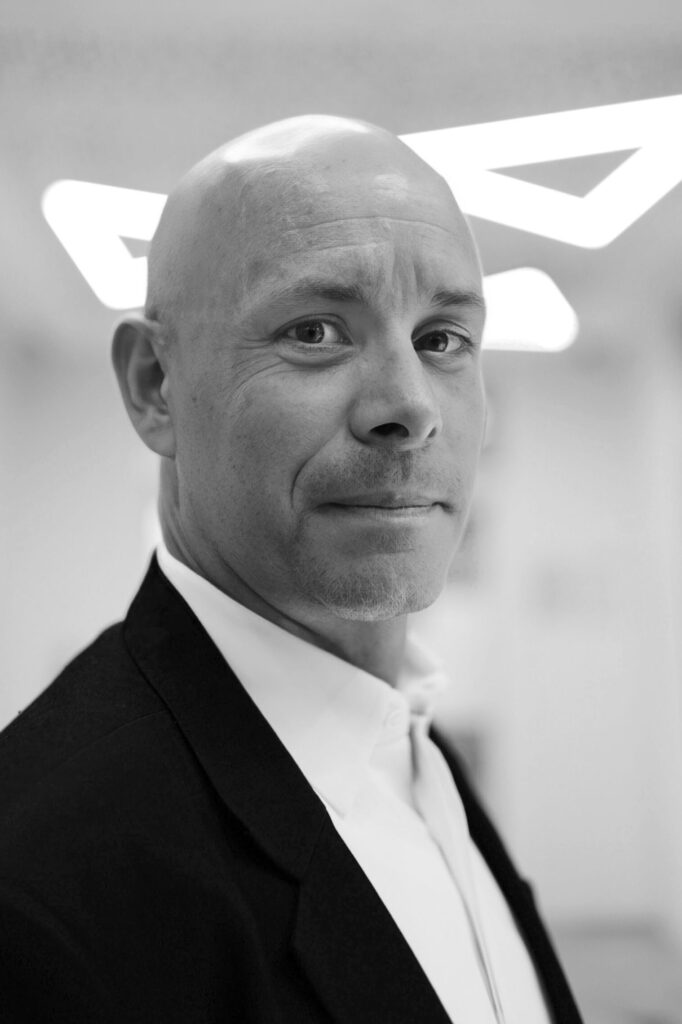

The cornerstone of the company’s technology transformation is a comprehensive overhaul of its IT backbone, including its Enterprise Resource Planning (ERP) system and adjacent applications. In an industry that still handles much of its business on bits of paper, Hapag-Lloyd is determined to digitalise every aspect of its operations and help customers access complex, world-spanning logistics services as simply as if they were booking and managing airline tickets.
A critical tool facilitating continuity during the IT overhaul itself, as well as empowering its digital future, is Intelligent Automation (IA): A digital workforce generated by Robotic Process Automation (RPA) and its integrations with other applications, assisted by machine learning and AI.
Hapag-Lloyd’s operations involve huge volumes of information transactions, whether that’s with customers, ports, its long chains of logistics partners and suppliers, or between internal parties. Historically, every one of those transactions has been labour for human hands, and often involving paper.
Mateusz Linda, Director of Automation & AI at Hapag-Lloyd, oversees the IA programme from the company’s base in Gdansk, Poland.
“When we have all the necessary technology components in place, we can deliver better on the quality promises towards our customers,” he says. “These are things like accurately releasing bills of lading, accurately invoicing customers, communicating booking information in a timely manner, always being accessible for them when they have a case, and so on. And by using these different technologies, we are able to do that better.
“Intelligent Automation is about combining multiple tools to help get to the business results that we want.”
A model for success
It is in Gdansk that Hapag-Lloyd established its RPA Centre of Excellence and chose its IA partner, SS&C Blue Prism, after exploring a range of potential options. SS&C Blue Prism, which famously pioneered robotic process automation when it was founded 23 years ago and coined the term RPA, presented Hapag-Lloyd with the best commercial terms, most flexibility, and most robust enterprise scalability, says Linda.
“Our organisation is structured very much in line with SS&C Blue Prism’s success framework and maturity model, ROM2. In the central hub we have the core team of analysts and developers, then we have the decentralised teams worldwide, trained by us
“ROM2 has been really instrumental in setting up the entire programme here. On the vision side, it’s really helped us to get that clarity. On the people side, we have followed the roles and responsibilities as they have been defined in ROM2, and on the governance side we have also been able to really secure the long-term stable, solid operation of the programme.”
Little more than three years in the making, Hapag-Lloyd’s automation journey has seen it grow from practically no RPA automation capability at all to a fully-fledged global organisation, stacked with expertise and providing 24/7 support, that is making a daily impact on every continent.
“Each and every year we managed to be 10 to 20% above the business case, so the entire RPA programme is definitely a huge gain for our company.”
– Mateusz Linda
Krystian Malec, RPA Technology Manager, was one of the first in the door as the company began to build its core automation team at the height of the COVID-19 pandemic. He says progress was rapid, with the team identifying automatable processes quickly and achieving 100 “bots” (digital workers, each fulfilling discrete end-to-end processes and returning that time to Hapag-Lloyd’s humans) in production within the first year.
“We’ve now had almost 200 in production,” he adds. “This is something we have accomplished with no speck of RPA in the organisation not that long ago. It’s very exciting.”
The results have been dramatic. One of the earliest projects Malec and his growing team took on was to automate the processing of key export paperwork – bills of lading – for customers’ shipments. An ambitious early undertaking and a key contributor to helping Hapag-Lloyd meet its new quality-service benchmarks, the automation would need to cater to the whole world, run 24 hours a day, and never take more than two hours.
“That was one that provided a lot of value in terms of process,” says Malec. “There were between 40 and 60 colleagues doing this work manually and now they are able to do better things within our Global Capability Centre, which provides standardised services across the globe. Our bot is essentially doing most of the export steps, end to end, for the business.”
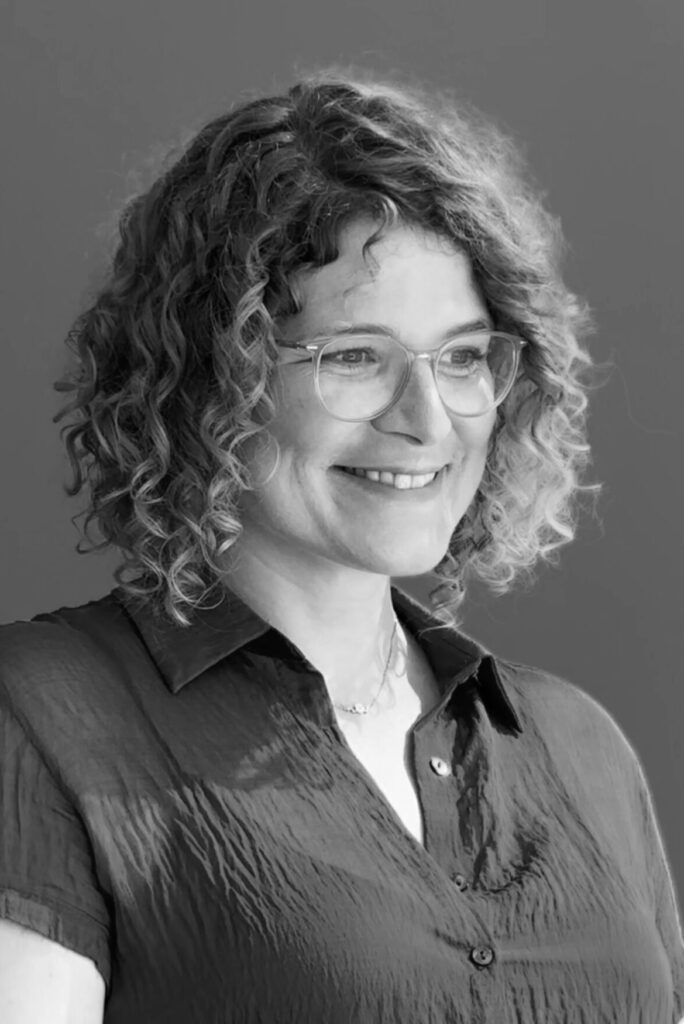
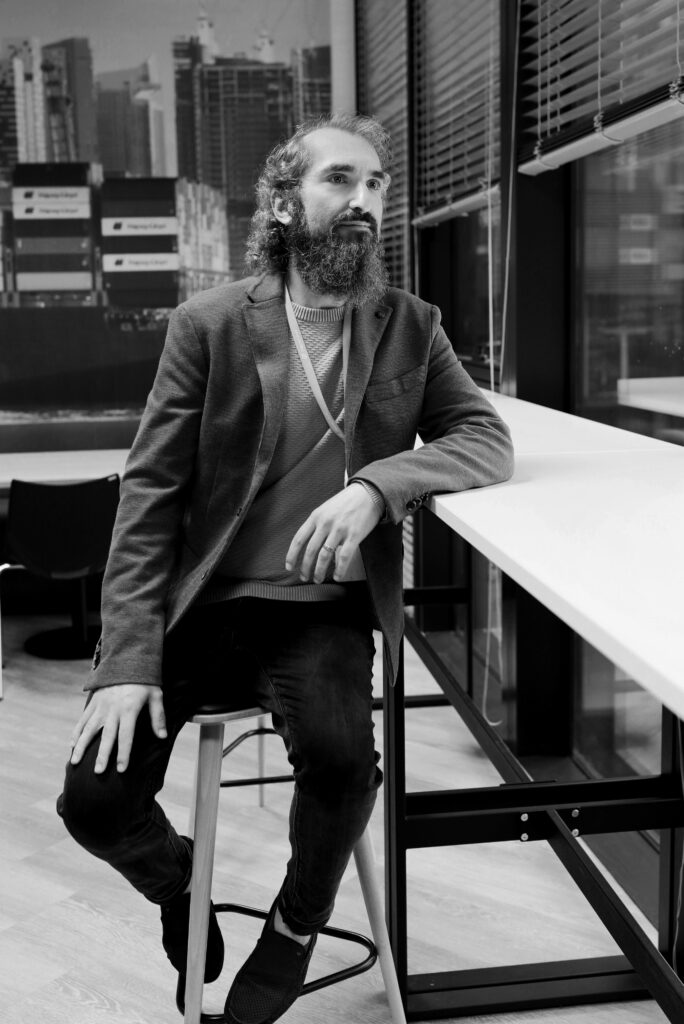
Malec says this particularly critical task is now completed around five times faster for customers worldwide.
Overall, the company estimates it returned a total of around 500,000 hours to the business in 2023, or the equivalent of over 60,000 days of human toil that can now be better deployed serving the business and its customers. Just two of Hapag-Lloyd’s digital workers are capable of processing 750,000 items a month.
Linda adds: “The entire RPA programme at Hapag-Lloyd is business-case driven. The main ingredients on the benefits side are, first of all, time saved for the company, and secondly monetary benefits – whether that’s hard dollars or risk mitigation.
“I’m really proud to say that we have always over delivered on these benefits. Each and every year we managed to be 10 to 20% above the business case, so the entire RPA programme is definitely a huge gain for our company.”
Hub and spoke
Just one year after Hapag-Lloyd began its IA journey, it won an award from SS&C Blue Prism for its successful implementation of its ROM2 framework. A key element of that model is centralising expertise and governance while cascading it across the wider organisation via a hub-and-spoke organisational structure.
Carolin Arens’ extensive job title – Director of Project Management & Process and Performance Support – describes well her role identifying opportunities for automation in her Germany and Central Europe region
“Our basis is sea transport, and very often we connect that with landside transport. We have a lot of customs and other processes that have to go hand-in-hand, and really integrate well, in order to make the supply chain work for our customers and their cargo. This is where the real challenge lies, and where technology and automation can really help,” she says.
Arens first encountered the power of automation shortly after taking over her new team at the company and running with a suggestion from a team member to explore IA as an alternative to laboriously filing work orders.
She recalls: “We went through the analysis, and we had great support. That’s when I realised the potential; it was fascinating. After that I couldn’t stop. Now all I can do is think about automation opportunities with the organisation.”
In that case, each work order involved a team member manually entering requirements into form fields, sending orders for approval, then matching them with invoices. Intelligent Automation, with the support of AI, now reliably compiles information from various sources and completes the process automatically, leaving the humans in the loop to focus on quality and safety.
“We had capacity gain as well as a quality gain, and that’s the most important thing. If we want to keep up delivering the best quality for our customers and keep the healthy gap to our competitors, these are the things that make the difference.”
Under Hapag-Lloyd’s operating framework, Arens and others in similar positions globally are working to feed the centre with new opportunities for automation. Her team documents and qualifies a process, identifies the return on investment, and then submits it for consideration against overall company objectives, any technical conflicts, and areas of priority.
“Luckily, we have been chosen quite a few times now,” says Arens of the process candidates her team has submitted.
Culture shift
Hapag-Lloyd’s success has been achieved not just because of building great technology and skills, but because the company has also understood a vital tenet of its operating model: it needed to manage change amongst its people carefully, developing a culture ready to make it work
“Automation helps you to improve your business all the time, but that also comes with the mindset,” says Verstraete
“You have to have the right mindset to use Intelligent Automation on one side, and on the other side you also need the people. You have to change your skills. One skill is to develop the bot, but another is to imagine it and interpret it and use that to your benefit. It is definitely a journey. “
Arens’ position on the frontline helps her to see the cultural ingredient of transformation up close.
“Our job is to bring automation to the organisation and work through any resistance to the unknown. We work through it by analysing processes, highlighting the potential for automation, and show what that means in terms of value-adding work for people,” she says.
“Working with automation is different, inspiring. It does make you think differently. It makes you start to see challenges as opportunities.
When Hapag-Lloyd defined its quality-driven strategy, it chose to display its progress towards its goal publicly, in detail, and hold itself accountable. Its award-winning automation team is working across the organisation to bring about the efficiencies and enhancements the organisation needs to achieve them.
Malec says he likes to think of the automation Centre of Excellence as the company’s elite problem-solving team, moving fast to deliver solutions to the business even as their IT colleagues continue to build a whole new infrastructure for the future.
“Intelligent Automation is with us to stay,” he says. “It’s here to help us accelerate, scale, streamline our processes in such a way that we can make those executive decisions at a faster rate. At the end of the day, our number one goal as an organisation is to be number one in quality. Intelligent Automation definitely supports that vision.”
Intelligent Automation in action at Hapag-Lloyd
01
Coping with Covid
Hapag-Lloyd set its entire Intelligent Automation programme in motion during the height of the COVID-19 pandemic, and in doing so played a vital role in helping the company navigate some extremely troubled waters.
Demand surged to unprecedented levels during the crisis, accompanied by huge amounts of disruption. Volume peaked to new levels again as the pandemic began to abate and the world unlocked.
“During the two, three years when COVID hit, one of our biggest problems was not even being able to accept new bookings. The demand was so high – the biggest in history,” says Mateusz Linda.
“With automation, we were able to relieve a lot of pressure that our company was under from customers. We freed up people’s time really to do their job, to do the more creative parts, being closer to the customer and more focused on quality and our promises.”
Surviving Suez
In March 2021, in the midst of a period of record-breaking demand for the shipping industry, one of the largest container ships in the world – the Ever Given – ran aground in Egypt’s Suez Canal, blocking it to all traffic. The result was the most serious disruption in more than 65 years to one of the busiest shipping routes in the world.
Almost 400 ships were stranded during the eight-day delay, and with them approximately $10 billion in trade. For Hapag-Lloyd, it represented a storm of emergency rescheduling, rerouting, and customer management.
Mateusz Linda: “Intelligent Automation really was a lifesaver for us during this incident.
“Our vessels either got stacked or needed to consider rerouting around Africa. It was, of course, quite some operational disruption.”
SS&C Blue Prism’s intelligent automation platform features reusable objects – specific actions that, once codified, can be reused by digital workers in any other process. This would become a vital weapon in Hapag-Lloyd’s arsenal, helping the team set up a solution to an enormous problem in less than 48 hours.
“Our business colleagues came to us saying they needed, over the weekend, to update more 50,000 shipments with appropriate estimated time of arrival dates. Intelligent Automation was here for us. Due to the scalability of blueprints and our setup, we were able to – literally in a day or two – come up with an automation that sorted out this business problem for us.”
02
03
Invoice Disputes
Invoices issued by Hapag-Lloyd can be as enormous in complexity as they are vast in number. A persistently burdensome overhead, particularly in times of high demand, are invoice disputes.
When a customer questions even a single line of a complex shipping invoice, they do so via unstructured text in emails. Administering those disputes has historically been an intensely manual and time-consuming process and, in every case, one that halts payments. Across a global shipping footprint, revenue stalled in invoice disputes quickly accumulates into tens of millions of dollars at any one time.
“What we managed to do here is I think a perfect example of an Intelligent Automation solution,” says Mateusz Linda.
“We married RPA with AI. RPA scans through all our mailboxes, picking up emails from customers. An AI module then determines the type of dispute and reads the information into our core system so it can then be handled by the relevant people.”
As early as 2020, Hapag-Lloyd was already automating more than 300,000 invoice disputes a year, and doing so with 90% accuracy.
Hazardous Cargoes
While transporting huge numbers of containers around the world features administrative burdens on a vast scale, the complexity of doing that with hazardous cargoes increases the load even further.
Hapag-Lloyd has centralised its process management for dangerous cargoes in Gdansk, Poland, where the company also maintains its automation Centre of Excellence. It means Krystian Malec and the automation team are able to get up close and personal with the challenge.
A significant proportion of the hazardous cargoes Hapag-Lloyd manages are shipped via specialist partners. Liaising with a third party, on top of handling much increased approvals and regulatory overheads, historically meant very large amounts of time-consuming manual administrative work.
“We need to work together with partners to make sure dangerous goods are properly checked, approved, and tracked,” says Malec. “Thousands of mails would be sent manually as reminders to partners. We digitised and automated them.”
Mateusz Linda adds: “We managed to automate a process that, on a daily basis, exchanges over 100,000 messages and approvals and confirmations between Hapag-Lloyd and our partners, which was very big workload on the team here.”
04
05
Sustainability
In Hapag-Lloyd’s own words, sustainability is anchored in its corporate strategy. It aims to reach net-zero greenhouse gas emissions from its fleet by 2045, with a 60% reduction by the end of this decade.
The company already offers a ‘Ship Green’ product that allows customers to book biodiesel with their shipments and reduce the emissions from the ocean legs of their transportation by up to 100%.
“We are very serious about sustainability, and even in this area we can have an impact with automation technology,” says Javier Verstraete.
“The teams who are working to calculate ship speeds and fuel consumption are using RPA, and beginning to use AI and NLP, to help reduce consumption. Automation already has a direct impact on emissions.
“Wherever you look, RPA is helping people to have and process more data and take better decisions. All areas of the company are using bots in some way, and now everybody is demanding it.”
Coping with Covid
Hapag-Lloyd set its entire Intelligent Automation programme in motion during the height of the COVID-19 pandemic, and in doing so played a vital role in helping the company navigate some extremely troubled waters.
Demand surged to unprecedented levels during the crisis, accompanied by huge amounts of disruption. Volume peaked to new levels again as the pandemic began to abate and the world unlocked.
“During the two, three years when COVID hit, one of our biggest problems was not even being able to accept new bookings. The demand was so high – the biggest in history,” says Mateusz Linda.
“With automation, we were able to relieve a lot of pressure that our company was under from customers. We freed up people’s time really to do their job, to do the more creative parts, being closer to the customer and more focused on quality and our promises.”
Surviving Suez
In March 2021, in the midst of a period of record-breaking demand for the shipping industry, one of the largest container ships in the world – the Ever Given – ran aground in Egypt’s Suez Canal, blocking it to all traffic. The result was the most serious disruption in more than 65 years to one of the busiest shipping routes in the world.
Almost 400 ships were stranded during the eight-day delay, and with them approximately $10 billion in trade. For Hapag-Lloyd, it represented a storm of emergency rescheduling, rerouting, and customer management.
Mateusz Linda: “Intelligent Automation really was a lifesaver for us during this incident.
“Our vessels either got stacked or needed to consider rerouting around Africa. It was, of course, quite some operational disruption.”
SS&C Blue Prism’s intelligent automation platform features reusable objects – specific actions that, once codified, can be reused by digital workers in any other process. This would become a vital weapon in Hapag-Lloyd’s arsenal, helping the team set up a solution to an enormous problem in less than 48 hours.
“Our business colleagues came to us saying they needed, over the weekend, to update more 50,000 shipments with appropriate estimated time of arrival dates. Intelligent Automation was here for us. Due to the scalability of blueprints and our setup, we were able to – literally in a day or two – come up with an automation that sorted out this business problem for us.”
Invoice Disputes
Invoices issued by Hapag-Lloyd can be as enormous in complexity as they are vast in number. A persistently burdensome overhead, particularly in times of high demand, are invoice disputes.
When a customer questions even a single line of a complex shipping invoice, they do so via unstructured text in emails. Administering those disputes has historically been an intensely manual and time-consuming process and, in every case, one that halts payments. Across a global shipping footprint, revenue stalled in invoice disputes quickly accumulates into tens of millions of dollars at any one time.
“What we managed to do here is I think a perfect example of an Intelligent Automation solution,” says Mateusz Linda.
“We married RPA with AI. RPA scans through all our mailboxes, picking up emails from customers. An AI module then determines the type of dispute and reads the information into our core system so it can then be handled by the relevant people.”
As early as 2020, Hapag-Lloyd was already automating more than 300,000 invoice disputes a year, and doing so with 90% accuracy.
Hazardous Cargoes
While transporting huge numbers of containers around the world features administrative burdens on a vast scale, the complexity of doing that with hazardous cargoes increases the load even further.
Hapag-Lloyd has centralised its process management for dangerous cargoes in Gdansk, Poland, where the company also maintains its automation Centre of Excellence. It means Krystian Malec and the automation team are able to get up close and personal with the challenge.
A significant proportion of the hazardous cargoes Hapag-Lloyd manages are shipped via specialist partners. Liaising with a third party, on top of handling much increased approvals and regulatory overheads, historically meant very large amounts of time-consuming manual administrative work.
“We need to work together with partners to make sure dangerous goods are properly checked, approved, and tracked,” says Malec. “Thousands of mails would be sent manually as reminders to partners. We digitised and automated them.”
Mateusz Linda adds: “We managed to automate a process that, on a daily basis, exchanges over 100,000 messages and approvals and confirmations between Hapag-Lloyd and our partners, which was very big workload on the team here.”
Sustainability
In Hapag-Lloyd’s own words, sustainability is anchored in its corporate strategy. It aims to reach net-zero greenhouse gas emissions from its fleet by 2045, with a 60% reduction by the end of this decade.
The company already offers a ‘Ship Green’ product that allows customers to book biodiesel with their shipments and reduce the emissions from the ocean legs of their transportation by up to 100%.
“We are very serious about sustainability, and even in this area we can have an impact with automation technology,” says Javier Verstraete.
“The teams who are working to calculate ship speeds and fuel consumption are using RPA, and beginning to use AI and NLP, to help reduce consumption. Automation already has a direct impact on emissions.
“Wherever you look, RPA is helping people to have and process more data and take better decisions. All areas of the company are using bots in some way, and now everybody is demanding it.”