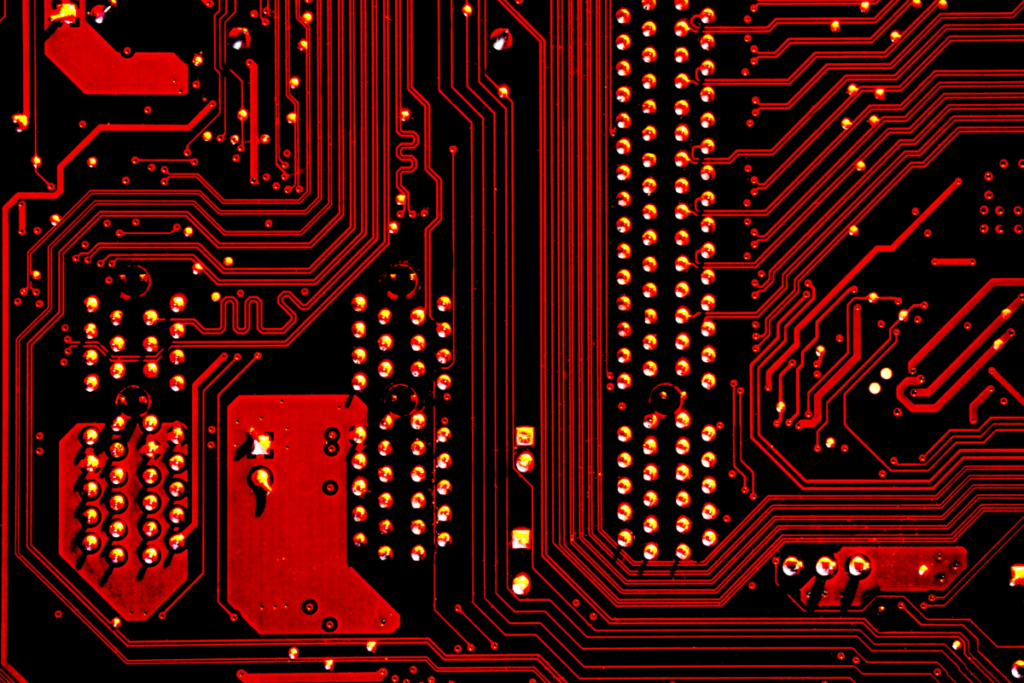
From machine learning to artificial intelligence (AI), advanced robotics and the Internet of Things (IoT), modern organisations are looking to technology to automate tasks and ground decision-making in data. It is an important enabler to business strategies targeting increased productivity and efficiency, cost reduction, staying competitive, and responding faster to market changes.
Organisations in sectors as diverse as retail, healthcare, banking and financial services are embracing automation solutions and new tech-savvy operational processes in every area of their operations – from finance and supply chains to regulatory compliance and company care. So much so that industrial automation investment is projected to hit $96 billion by 2030.
It’s not just large enterprises that are investing in automation solutions – 88 percent of small businesses say automation enables them to compete on a level playing field with larger companies, while 66 percent say it’s become indispensable for running their business.
The industrial sector is all too familiar with the concept of automation as a driver of productivity. However, the arrival of Industry 4.0 technologies has triggered a transformational shift that’s seen manufacturers leverage connectivity, advanced analytics, automation and advanced manufacturing technologies to rewrite the rules of production.
Driven by a myriad of interconnected mega trends that include enduring global supply-chain issues, a growing scarcity of skilled workers and new environmental regulatory demands, manufacturers are using next-generation industrial automation to contain costs and enable more efficient and sustainable operations. This involves initiating on-demand logistics processes and smarter inventory planning, as well as rethinking how assets are managed and maintained. The goal is to prevent machine failures and connect people with the data-driven insights they need to maximise operational effectiveness.
The journey to predictive maintenance
Predictive maintenance has been top-of-mind for industrial organisations ever since IoT made it possible to automate the collection of real-time data feeds from equipment and machines. By combining this information with historic maintenance data and service reports, it becomes possible to spot impending asset failures and know in advance when hard-to-reach assets need fixing.
In addition, organisations can connect and orchestrate every aspect of their maintenance environment by integrating parts management, inventory management and the assignment of work orders for preventative and corrective maintenance actions.
Predictive maintenance generates some significant real-world gains for industrial firms. Alongside generating operational cost savings of up to 40 percent compared to preventative maintenance, businesses benefit from a 50 percent decrease in equipment downtime together with a 20 percent increase in asset lifespan. A predictive maintenance strategy also enables manufacturers to drive sustainability practices that reduce waste and emissions and improve energy efficiency.
Unsurprisingly, investment in predictive maintenance solutions is set to grow substantially in the next five years, with the market growing 35 percent to hit $47.8 billion in 2029. But if asset managers are to maximise the benefits of their investment in these connected reliability technologies, they’ll also need to ensure they automate their critical enterprise asset management (EAM) workflows. In doing this they can streamline tasks, track and manage the lifecycle of mission-critical assets and acquire the visibility at scale that’s essential for making data-driven decisions.
Intelligent enterprise asset management – optimising maintenance, and more
Operations and maintenance leaders need to understand when and under which conditions enterprise assets will fail, so they can take immediate action and reduce the impact on production environments. The good news is that today’s intelligent EAM systems combine capabilities like AI-powered remote monitoring, machine learning, automation and predictive maintenance technologies in a single platform to achieve all this and more.
By delivering insights into maintenance needs at an individual asset level, EAM systems enable maintenance teams to pinpoint the maintenance needs of every individual asset. By extension, this brings additional insight into which assets require the most routine repetitive maintenance. This means that low-value tasks like meter registrations or machine maintenance scheduling can be automated, and IoT sensors can be used to trigger maintenance actions based on real-time data.
Providing a single source of truth for all asset performance and energy consumption, today’s EAM systems enable maintenance teams to initiate the condition-based and predictive maintenance procedures that are key for driving down asset costs and carbon footprints, while extending asset life cycles. These systems often feature digital, paperless workflows and procedures. They enable maintenance teams to monitor and proactively optimise the performance of assets and take corrective action to prevent downtime.
By connecting machines, people, and systems it becomes possible to plan interventions more effectively and streamline maintenance processes. For example, when Recticel Insulation took the decision to deploy EAM software at its Belgian site, it was able to replace 30 applications with a single system that now handles all its maintenance processes, including work orders, preventative maintenance and equipment management in a streamlined and automated manner.
Similarly, when Rockfon – part of the ROCKWOOL Group – implemented an EAM system to gain better visibility over its maintenance operation and enhance interdepartmental communication and collaboration, it was able to leverage real time access to critical data to reduce the incidence of human error in maintenance tasks and improve safety across the factory floor.
Centralising asset information and consolidating operational applications so that decision makers can stay on top of asset performance to reduce failure rates, manage risks, and avoid unnecessary costs is only the beginning. EAM systems also provide the targeted multi-layered automation and analytics that manufacturers need to be in control of their complex production environments. This includes handling activities like inventory monitoring and parts ordering and distribution in real time.
Industrial firms know to their cost that inaccurate or outdated asset data can lead to difficulties in managing spare parts and inventory levels. This is likely to have a major knock-on effect on the scheduling of maintenance activities due to the likelihood of stockouts. However, by automating their parts tracking and ordering processes, industrial firms can ensure they always have the right amount of the right stock on hand to repair and fix faster. Even better, they can fine-tune their stock management processes in line with FIFO (first-in, first-out) or LIFO (last-in-last-out) methodologies to ensure the right stock is always issued to the right engineer, at the right time.
The implementation of a modern EAM system has enabled Gatwick Airport to transform the lifecycle management of its billion-pound asset base and align its maintenance processes across multiple functional teams. Today, all assets are created, managed, maintained and replaced with pinpoint accuracy. Individual teams can now confidently collaborate and access all the real-time and accurate management information they need to work more effectively, together.
The future of reliability and performance – EAM automation
While an EAM system might help organisations to manage their day-to-day operations, it also revolutionises how companies allocate and optimise their operational assets and resources. For asset-intensive industries like manufacturing, EAM solutions make it possible to execute, track and optimise how they inspect, track, maintain and repair industrial plants and equipment and handle things like parts management and resource scheduling.
EAM software streamlines and automates asset management processes by providing a centralised platform for tracking asset data and analysing performance metrics. This delivers real-time insights that manufacturers need to make informed decisions. In turn, this will help with optimising asset utilisation, reducing costs, and extending asset lifecycles. Whether it’s maintaining accurate inventory records, automating maintenance workflows, or enhancing maintenance practices to improve overall efficiency, EAM software plays an instrumental role in powering operational success.
What’s more, manufacturers can use EAM systems to deploy digital twins, using real-time data and simulations to optimise tool calibration, load levels and cycle times, and determine when and where preventative maintenance or repairs will be needed.
One thing is for sure, while innovations such as robotics and autonomous machinery hold great potential, human workers still need to make sense of all this data to uncover potential problems and determine where the pain points lie. Therefore, getting the right information to the right people, at the right time, is imperative.
Automation is set to change the manufacturing landscape for years to come. The key to unlocking its full potential lies in having a centralized EAM platform at the core. This will turn automation into a powerful driver of sustainable growth and operational excellence.
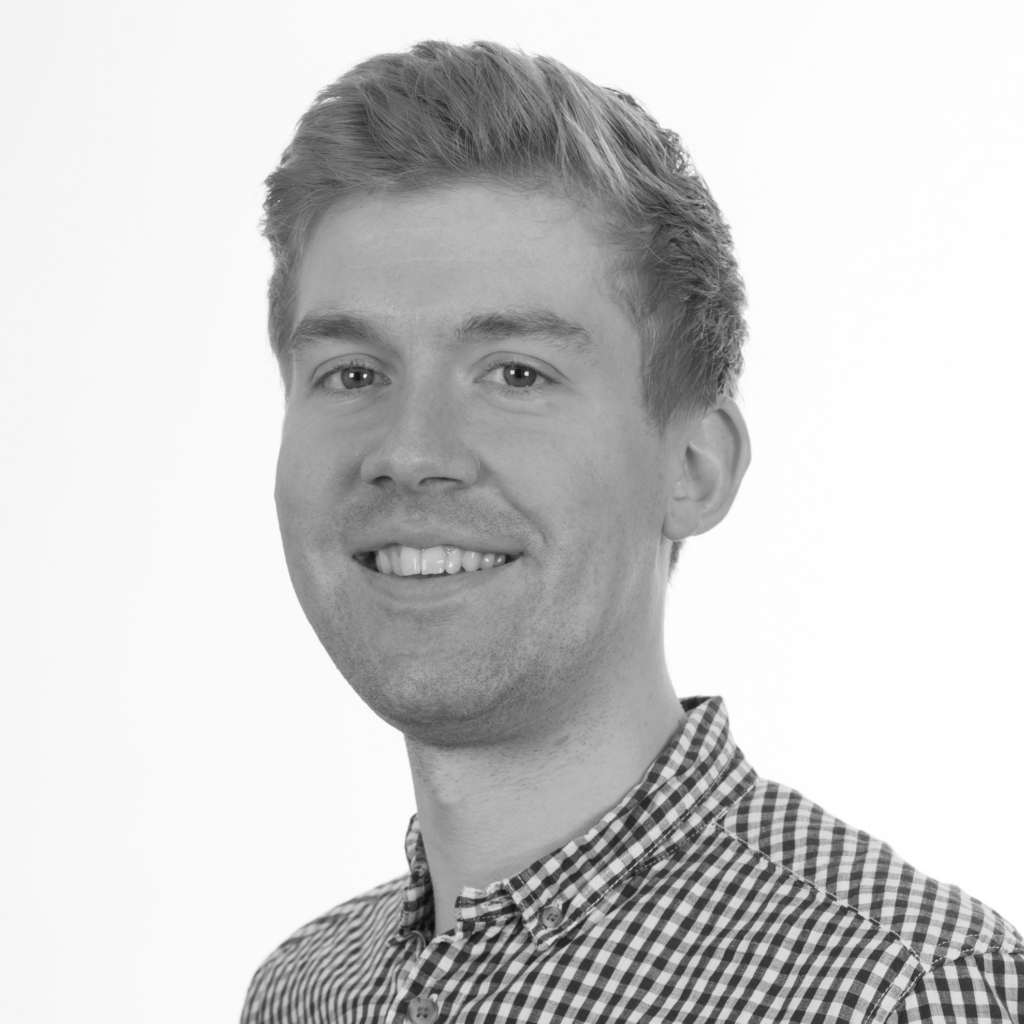
Berend Booms
Berend Booms is Head of Enterprise Asset Management Insights at IFS Ultimo.