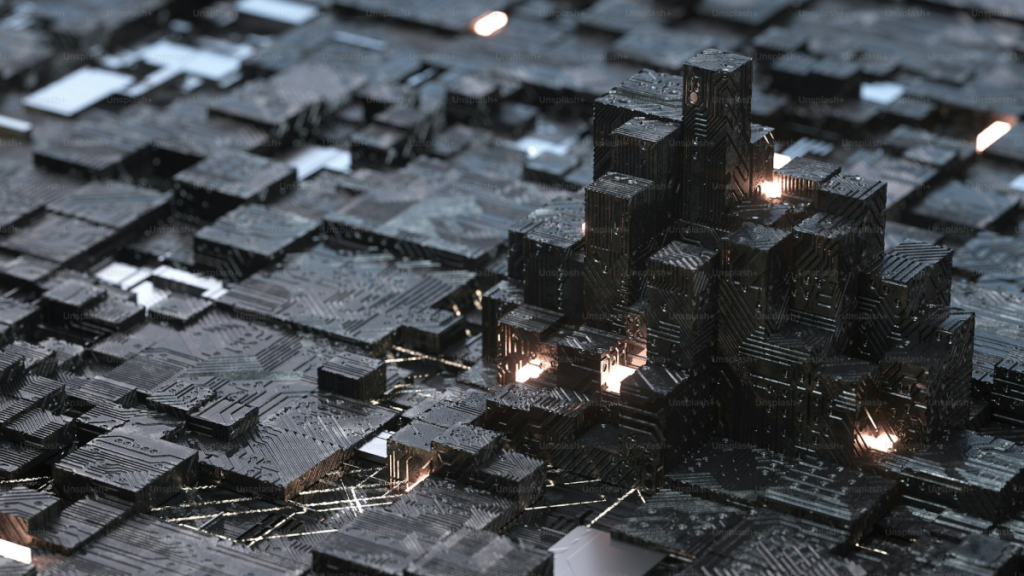
It’s no secret that artificial intelligence (AI) has the potential to transform workflows as we know it. This is particularly true for engineers, designers, and others who leverage technologies like simulation engineering to bring innovative products to life. Bringing AI into the fold can accelerate design and optimisation, especially for industries in which accuracy and efficiency are critical, such as high tech, automotive and aerospace.
Broadly speaking, AI-enhanced simulations are beneficial for several reasons. The first is speed; AI can analyse past simulations to quickly identify complex patterns while incorporating new information to vet relationships within the data. Secondly, AI can democratise simulation by making it more accessible to non-technical employees through user-friendly web-based applications. In addition to this, AI simulations enable the integration of multiple models to provide thorough representations of complex systems, giving individuals greater visibility into a product. Finally, leveraging AI simulations enables an iterative engineering process, allowing designers to improve their designs with less constraints.
With these benefits in mind, let’s look to some real-world examples of how integrating AI and simulation can optimise product design and further innovation.
Conducting thermal analyses in chip design
Chip design is a notoriously complex process that requires advanced engineering. It also usually involves dealing with nonlinear, unexpected behaviour. Simulation is already helping alleviate chip design challenges by offering insight into electrical, thermal, and structural characteristics to accelerate the overall design and verification process, and improve efficiencies.
In spite of this, engineers can still face hurdles when leveraging simulation on its own. For instance, the large number of elements in chip modelling mean that any slight modifications or errors significantly increase simulation time. And an additional challenge is successfully mapping spatial distribution uncertainty and variations in chip parameters, including die size and heat transfer coefficient (HTC) values.
Generating accurate predictions can be crucial in helping engineers assess chip thermal reliability earlier in the design process, and ultimately increase their efficiencies. This is where AI-infused simulation comes in; by training a model on specific simulation datasets, it can predict relevant outcomes to support the overall design process. For example, if engineers created an AI model that was based on thousands of diverse chip thermal simulation datasets, it can quickly predict a temperature distribution map and thermal critical locations. By complementing simulation with AI, engineers can expedite the development lifecycle for next-gen chip design.
Ensuring structural safety in jet engine brackets
Integrating AI into the simulation process isn’t just helpful for thermal analyses. In aerospace applications, structural analysis and design validation are imperative to ensuring an aircraft is safe for take-off. And this doesn’t just apply to larger components; even elements as small as jet engine brackets must be robust, as they support the weight of the engine itself.
As aircrafts continue to evolve, developing new jet engine bracket designs that meet weight and robustness structural requirements and constraints can prove challenging. As a starting point, engineers can look to previous design iterations that have been successfully simulated and validated. And to build on this, they can integrate an AI model that has been trained on a variety of different and topologically diverse bracket designs. As the model retains the data from past simulations, it can quickly predict the behaviour of a new shape; furthermore, it can be retrained with new sample designs later down the line to ensure it continuously captures new insights and refines its predictions.
Using AI simulation for structural analysis not only reduces material waste but makes failed designs valuable. Every iteration is a source of knowledge and helps both the model and the engineers understand the best practices when designing a jet engine bracket. And this ultimately enables them to design an optimised product.
Evidencing aerodynamic performance in vehicles
Leveraging AI simulations are as useful for ground applications as they are for airborne products. In the automotive industry, environmental regulations around emissions – like Euro 7 – are becoming increasingly front of mind for carmakers. Part and parcel to this is needing to assess and evidence aerodynamic performance of vehicles to ensure they are meeting standards.
Engineers can look to physical wind tunnel testing, but this approach can have drawbacks including high costs and time-constraints. To cut development times, engineers can turn to simulation to quickly assess electric vehicles in a cost-effective manner. AI complements this approach by drawing on variations in, for instance, car exterior shape as well as topological changes, such as a rear mirror, ski rack, and spoiler. Then, it can predict aerodynamic performance to ensure that designs are both optimised and validated.
By introducing AI simulations into the design process earlier on, engineers can incorporate fast and meaningful aerodynamic predictions throughout all stages. As such, they create and evidence a better product, that meets environmental regulations, in a shorter period.
A match made in engineering heaven
AI and simulation already deliver a host of benefits as individual tools, so bringing them together to maximise their value is a natural next step. With this approach, engineers can overcome physics and engineering challenges, and organisations can improve on workforce efficiencies, cost savings, and development times, to close the gap between design and reality.
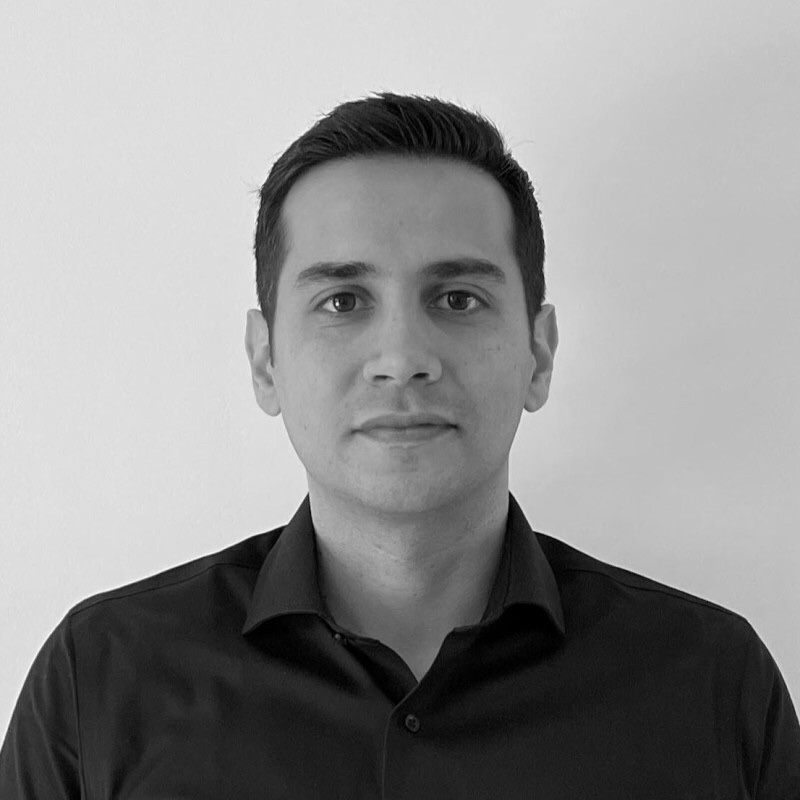
Mazen El Hout
Mazen El Hout is Senior Product Marketing Manager at Ansys.