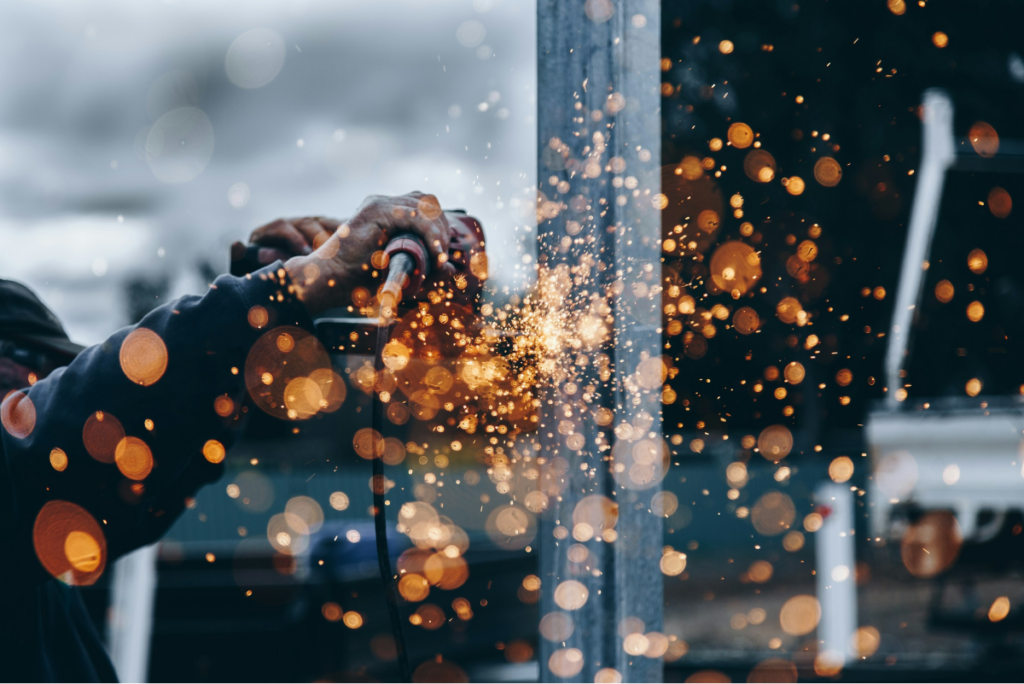
Five industry experts explore the technology trends that will shape the future of secondary industries, from construction to manufacturing, and what’s on the minds of technology leaders.
Jason Law - Group IT Director, Avant Homes
For technology leaders, the rising importance of IT sustainability will be a key priority for 2025.
Those within senior tech positions will need to ensure they fully understand the regulations around IT sustainability and the action required to reduce carbon emissions on behalf of their organisation.
As part of this, identifying, navigating and implementing the necessary criteria set out across a multitude of legislative publications will become a business-critical task.
While construction – and specifically housebuilding – tends to retain more traditional operating methods compared to other, more digitally advanced sectors, leveraging technology to minimise carbon emissions will have significant importance.
Transitioning to cloud-based systems is a logical step to take in this direction. Not only does this reduce physical hardware but also improves energy efficiency, aligning with both sustainability goals and cost-saving initiatives.
Conducting thorough evaluations of existing and prospective IT suppliers’ sustainability credentials can also help reduce or prevent second-hand carbon footprint contributions stemming from the supply chain.
In line with this, the need for transparency surrounding green initiatives is also apparent. Organisations and their technology leaders need not just talk about their steps toward sustainability but provide demonstrable evidence of their efforts.
A common misconception is that sustainable practices will always result in a financial or operational sacrifice. In reality, the sustainable option is oftentimes the most resourceful one, too.
Finding this equilibrium between optimising business performance and construction timeframes, as well as maximising sustainability efforts, will be a core focus for the construction sector’s technology leaders over the coming year.
Markus Nispel - CTO EMEA, Extreme Networks
As technology continues to play a transformative role in manufacturing, several key trends are likely to shape the priorities of manufacturing decision makers in 2025. Among these, the adoption of zero-trust security models will be paramount as manufacturers increasingly embrace Industry 4.0 technologies. With more connected devices and data flowing through smart factories, the need for robust cybersecurity measures has never been more critical.
Zero-trust assumes inherent untrustworthiness, a contrast to traditional security methods that take a secure perimeter approach to access control, using an outer layer of defence to protect a network and then assuming all users and devices are trustworthy once initially authenticated. With manufacturing often ranked first as a target industry for attackers, this outdated approach is unable to effectively protect networks from bad actors from the inside. Therefore, we can expect zero-trust to become the go-to security approach in 2025, significantly enhanced by the integration of AI technologies.
Beyond security considerations, the manufacturing sector is experiencing a growing focus on reducing operational costs and improving efficiency. This has created a need to address the application proliferation that has developed over the last decade, leading to increased complexity and costs. Each vendor and application typically comes with its own licensing model, which can complicate matters for customers who must familiarise themselves with multiple systems. The trend towards platformisation aims to reduce this complexity and costs for buyers and users alike, with industry leaders increasingly recognising the importance of integrating AI, networking, and security into a centralised framework. This trend aligns with our recent survey where 88% of CIOs and IT leaders expressed a desire for a single integrated platform to streamline operations, enhance productivity, and address emerging cyber threats. As manufacturers expand their digital capabilities, simplifying their deployments will play a critical role in maintaining robust zero-trust security and optimising operational efficiency.
With robust and secure network infrastructures unifying these components, manufacturers who embrace platformisation and invest in these advancements will be at the forefront of the evolving industrial landscape. This strategic approach will ensure they remain competitive and thrive in 2025 and beyond.
Steff Wright - Chairman, Gusto Group
Unfortunately there hasn’t been – and still isn’t – enough enthusiasm for going over and above basic building regulations, stemming from a lack of government incentivisation for companies to do more than pay lip-service to sustainable commitments. It’s only a few small housing builders who are taking the lead on technologies that can push us towards zero carbon targets; who are building to higher standards than the PLCs.
Practices such as councils only partnering with businesses that can prove their green credentials (for example through the B Corp movement) or a tax on carbon intensive materials, would prompt builders to pay more attention to the materials they’re using and their processes. Fortunately, initiatives like the AECB (Association for Environment Conscious Building) are attracting members and driving sustainable practices across the sector, as well as facilitating partnerships that can pave the way for more regulations around embodied carbon and other metrics.
Gusto has been finding ways to make these developments commercially viable for the last 25 years and many of our customers have experienced what it’s like to live in a house augmented by the technologies that are going to shape the future of the sector. 150mm wall cavities allow for three times as much insulation as minimum standards; infrared panel heating systems remove the need for air-source heat pumps because the energy requirement is minimal; a power diverter linked to photovoltaic panels on the roof moves excess power straight into the hot water cylinder, so you’re effectively using your hot water cylinder as your energy store; rain-water harvesting; heat recovery ventilation systems; use of natural materials like hemp; all of these have worked well for us.
In fact, we’ve worked with the University of Lincoln to conduct post-occupancy evaluation and interview owners in one of our developments. They said they were “beyond impressed with [their] eco-friendly house”. The houses had “a mega thermal advantage, and stable warm temperature all year round”; were “so well-insulated that we hardly need any heating”; and, in some cases, had “zero electricity cost”. Owners have described our properties as “the next generation of Eco Homes”.
Over and above that, though, our main triumph has been the development being described as a “lovely community”. That’s what developers need to aspire to; they need to move past monetary gains as the sole driver of building houses and exceed minimum standards rather than simply meeting them. Yes, using cheaper materials is the most financially lucrative option but the current model doesn’t generate any drive for innovation. We need to look at value in different terms; designing houses that are appealing to live in, with the wider community and planet in mind, adds value to people’s lives.
Frances Sneddon - Chief Technology Officer, Simul8
Digital twins and simulation are essential technologies. However, in 2025 we expect to see an increase in the number of organisations combining the two to unleash the power of simulation-powered digital twins.
A regular digital twin will provide a static representation of a system’s current state, but what they don’t do is look forward or predict future events. By combining simulation technology with the real-time capabilities of digital twins you can run scenarios forward by weeks, or even months, giving you more time for corrective action. It’s a new type of highly accurate forecasting and planning which is invaluable in sectors such as manufacturing, engineering and automotive production.
For example, simulation-powered digital twins help organisations spot continuous improvement opportunities more frequently. This includes smaller, incremental changes that might otherwise go unnoticed. It’s like having a live dynamic playbook that identifies peaks and troughs in operations. The digital twin gives you the most effective processes to implement to cope with fluctuating demand.
A key advantage of this technology is it supports forward-looking predictions and retrospective analysis, helping organisations understand past problems and prevent future ones. The more time process owners have to optimise operations, the greater the timeframe for corrective actions.
It also encourages a reflective mindset, allowing teams to make proactive adjustments rather than rely solely on reactive problem-solving. Traditional continuous improvement methods will always be important, but integrating simulation-powered digital twins offers a more responsive, data-driven way to optimise operations in real time.
Simulations have moved from being used for one-off capital investment-type decisions to making weekly, daily and hourly operational decisions. This advancement comes as processes have become more complex and granular, so we need assistance in understanding those details when making decisions. We now have the data and systems to involve simulation-powered digital twins in every one of these important decisions, meaning organisations can reach value quicker to gain a competitive advantage.
Whereas before a simulation might have been focused on overarching objectives, like improving throughput or removing bottlenecks in a system, the combination with digital twins also makes it possible to demonstrate the most effective way to implement a process at a specific point in time.
Bas Beemsterboer - Strategy Director, Hexagon
Industrial companies have been early adopters of AI for predictive maintenance and condition-based monitoring. In the UK, more than 60% of decision-makers report that they have already implemented AI for these purposes, with another 30% planning to do so soon. While these tools have helped increase reliability, they have not eliminated unplanned downtime, which still costs manufacturing companies a staggering $50 billion annually.
The reasons are many; a crucial one is that manufacturers have a wealth of asset data – such as EAM work history, costs, failure records, and condition and process data – but they often lack critical visibility into risks, potential failures, and opportunities. As a result, they struggle to identify which assets are over-maintained or to optimise maintenance plans for risk and resource efficiency.
At a time when manufacturers face margin pressures and seek ways to reduce maintenance costs, Asset Performance Management (APM) is set to play a key role in resolving these challenges.
Closing knowledge gaps into risk, performance and opportunity
APM seeks to help organisations safely achieve optimal value from assets, at the lowest sustainable cost, while observing the risk profile of the business. This is made possible by a lucid and objective view of asset risk, cost, performance, and opportunity. To achieve this clarity, organisations need ways to close their knowledge gaps – in other words, using the information that they already have to generate the insights they are lacking.
This process demands a strong knowledge base. For instance, Hexagon’s APM solution leverages an embedded asset twin library with over 200 common equipment types and thousands of associated failure modes and protection strategies, developed by maintenance and reliability experts. Such a library enables industrial organisations to quickly implement failure prediction and optimal maintenance strategies, accelerating value realisation.
With this knowledge in hand, manufacturing companies can identify where they are over-maintaining and under-maintaining, find out their blind spots by identifying under-performing assets, and achieve incremental capacity utilisation.
Anticipating the generational shift by consolidating internal and external expertise
In the face of a generational shift, APM also helps manufacturers balance human expertise with digital models and analytics. The goal isn’t to replace the knowledge of subject-matter experts with automated insights, but to combine them. APM provides a platform to capture SME knowledge, drive organisational learning, and ensure continuous improvement.
The advantage of this approach is its ability to constantly test and refine strategies, such as running simulations with historical data to fine-tune models and operationalise asset twins.
For companies under pressure to cut maintenance costs without increasing risk or compromising performance, this structured and flexible approach to managing asset strategies will be crucial. It enables them to minimise unscheduled downtime, optimise spending, and help all stakeholders find the best balance between risk, cost, and asset performance.